What is PlanMaster?
PlanMaster is a finite capacity scheduling software specifically designed to meet the complex needs of production planning and scheduling in industrial settings
Each adjustment on the chart is carefully managed to align with all relevant constraints, ensuring a comprehensive and error-free schedule that considers multiple factors. Assignments and modifications are effortlessly executed through a drag-and-drop interface on a Gantt Chart, which visually represents work timelines and resource occupancy. This approach not only enhances usability but also provides a robust environment for visual analysis

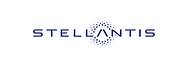.png)

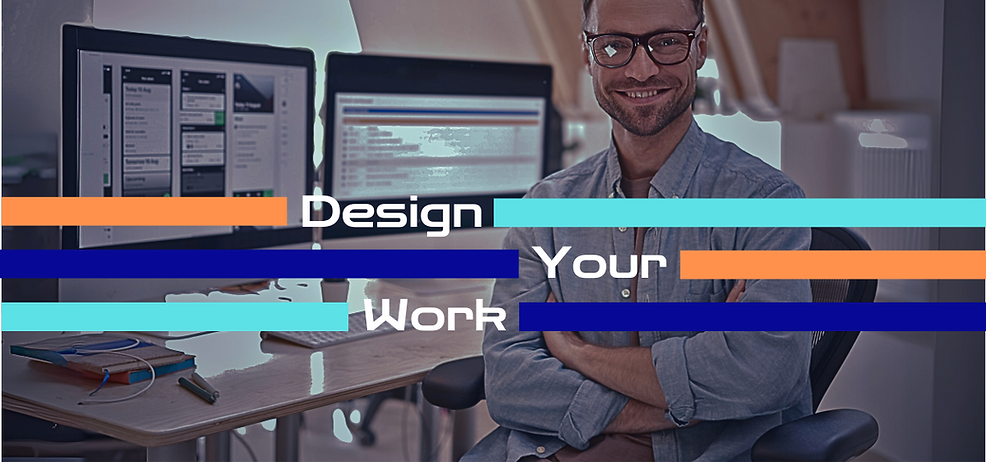.png)


PlanMaster is built for seamless integration with
ERP, MES and other systems supporting your business processes, while also functioning effectively as a standalone solution. Its flexible design adapts your production planning and scheduling processes to your existing infrastructure and its system-independent capabilities offer tailored solutions to meet the unique needs of your company.


What can you do with PlanMaster
Scheduling
Schedule using your machinery, personnel, and stock constraints.
Finished / Semi-Product Management
You can consider your stocks when planning for finished and semi-finished products. (You can make prioritization more accurate, you can minimize your product/semi-finished product waiting times by avoiding productions made earlier than necessary)
Operation Attribution
You can associate operations starting together or starting after the other is completed (“start to start” or “end to start”), and you can define specific delay predictions to these relationships. (As your associated operations will act within the rules you set, the possibility of making mistakes is eliminated)You can collectively manage your operations according to your relationship rules. (You can rearrange your plans in minutes)
Automatic Setup Management
You can automatically reflect the setups you define on the basis of references and the setup relationships between references to your plans. (With the automatic setup account, you can instantly see the effect of the changing sequences on the plan; you can quickly decide whether it is advantageous to manage by dividing the works)
Operation Planning
While planning your operations, you can assign different units/hours (uph) to your resources on a machine basis, and you can plan by taking these differences into account. (In this way, you can instantly evaluate the effects of using alternative sources and make the right decision) You can create different shift cycles (double shift, triple shift, etc.) for your machine groups, and use the number of people in these shifts as a factor in your plans. (You can manage your plans not only in terms of machine capacity, but also in terms of workforce capacity)
Restrictive Manufacturing Elements Management
Include your restrictive parameters such as Mold / Tool / Fixture in the plan. Use your restrictive production elements other than machinery and labor as parameters in your plans..
Non-Production Activity Planning
Plan your non-production activities such as Breakdown / Maintenance / Trial / Training. Apart from production, you can reflect the influential factors in your plans.
Break / Stop Planning
You can reflect your daily, weekly, monthly, yearly routine breaks and stops to your plans.
Real-Time Gantt Management
Change your job quantities in real time on Gantt. You can revise the values such as the amount of work / cycle time / personnel that you define by default, specific to that work piece.
Monitoring Production Plans
Observe the plans for the individual production stages together. You can manage the plan you have created by seeing it with the previous and next plan levels. (By seeing the plans of more than one level together, you can see the delays with the previous and next stages. It prevents delays and time losses, and you can synchronize between the plans).
Plan Quality Measurement
You can internally compare the scenarios you derive from the "key performance indicators" (kpi) (total job time, total setup times, machine efficiency, etc.) that you have determined. (By creating alternative plans, you can choose the most suitable one among the alternatives in the light of the data. You can analyze the effects of the changes made on the plan numerically)

Why Do We Need Scheduling?
Production planning, typically managed within an ERP system, is a high-level, strategic process that determines what, when, and how much needs to be produced over a certain period. It forecasts demand, organizes resources, and creates work orders but generally assumes an unlimited capacity and ignores real-time constraints.
Scheduling, on the other hand, is a more granular process that takes the production plan and sequences tasks with real-world constraints in mind. Unlike production planning, scheduling considers factors like machine availability, shift patterns, setup times, and unexpected delays. This stage ensures that each work order is aligned with actual resource capacity, optimizing workflow and adapting to changing conditions to improve efficiency and meet delivery timelines.
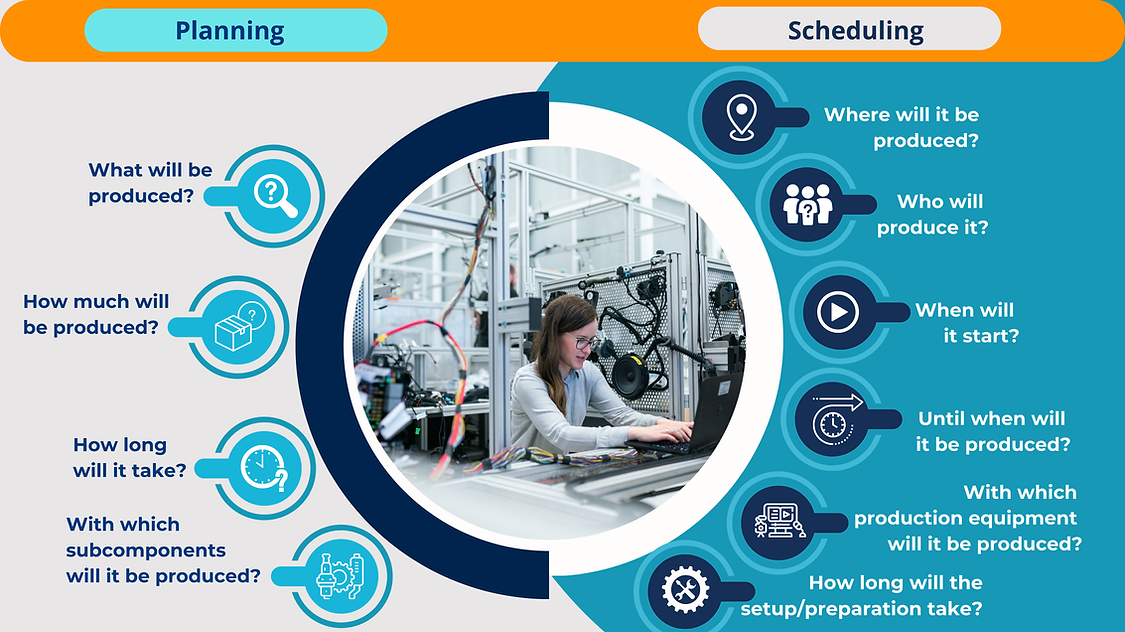
Increasing Capasity Utizilation
Reducing Stock
Increasing
On-Time Delivery Rates
Production scheduling optimizes capacity utilization by aligning work orders and resource use, minimizing idle time, and ensuring efficient operation of machines and workforce. By reducing unnecessary stock accumulation, scheduling enhances cash flow and lowers stock costs through demand-based planning. Well-organized production stages prevent delays, streamline workflow, and increase operational efficiency, enabling timely deliveries aligned with customer demands.
Limitations of ERP Systems in Realistic Production Scheduling
Although all ERP systems, including the most well-known and used ones in the industry, allow to manage the basic supply chain and production operations in enterprises, this management is carried out in a fiction that assumes endless capacity, where there are no constraints, due to their scope.The main reasons why ERP outputs cannot be used directly are:-Planned work orders are set up with production times independent of quantity.-Efficiency differences between production sources are not taken into account.-Factors such as differences in preparation times (setup), breaks and postures cannot be taken into account.-Restrictive factors such as mold, apparatus, fixture are ignored.- Considering the situations that develop outside of planning and require revision (order changes, malfunctions, lack of personnel, mold / apparatus failures, etc.), it is very difficult and time consuming to manage especially unexpected situations with standard methods.

Why PlanMaster?
The main development purpose of PlanMaster is to provide a fast, dynamic and reactive planning environment where data can be managed relationally and visually.
Relationality
Visibility
Ensuring that every assignment made on the chart is controlled together with all constraints.
All assignments and changes are made by drag and drop method with a gantt chart where job times and resource occupancy are visualized.
PlanMaster brings together all the necessary parameters for your planning within these two basic principles and offers you a working environment that allows you to make accurate, fast and measurable plans. It is easy to use and interactive.

PlanMaster: Bridging ERP and MES for Optimized Production Scheduling
PlanMaster is designed to seamlessly integrate with ERP and MES systems, enhancing your production scheduling process by bridging long-term planning with real-time shop floor management. Positioned between ERP, which handles high-level resource planning and production orders, and MES, which manages real-time manufacturing data, PlanMaster optimizes workflows by generating production schedules that adapt to actual conditions and capacity constraints.
PlanMaster imports MRP results from ERP, issues production orders back to ERP, sends optimized schedules to MES, and continuously receives real-time updates from MES on the actual production status. By accounting for key factors like setup times, machine availability, and resource efficiency, PlanMaster ensures that operations remain efficient and adaptable, reducing idle times and increasing productivity.
%20(English)%20(3).png)
